Commercial Equipment Rebate
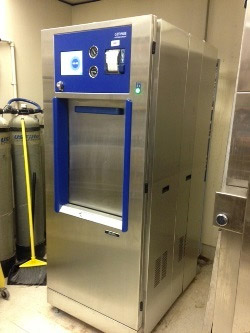
New Updates as of 6/25/2024
Businesses and commercial facilities with a SFPUC water service account may qualify for rebates to upgrade or replace a wide range of indoor equipment that uses water for cleaning, washing, sterilizing, cooling and other commercial purposes. Eligible projects must save at least 74,800 gallons* or more a year to qualify and be installed at the property served by the water account. Properties may apply for multiple rebates if they are replacing more than one piece of qualifying equipment. *748,000 gallons = 100 cubic feet (ccf) of water. One ccf = 748 gallons .
Qualifying Commercial Equipment Projects
This program offers two types of rebates:
1) Metered Water Savings Equipment Rebate.
This rebate covers custom, site-specific projects that can be metered to verify water savings, typically by an in-line meter. The SFPUC will calculate the rebate based on the metered water savings at a rate of $7 per 748 gallons of water saved over an estimated 10-year project lifespan, up to 100% of the equipment costs, not to exceed $750,000 per rebate. This rebate requires an onsite inspection by the SFPUC before and after the equipment is installed. The SFPUC will calculate the rebate amount approximately three months post installation after sufficient metered water use data is available. This time frame may vary depending on the project’s water consumption patterns. The Metered Water Savings rebate will be issued after water savings verification and upon receipt of all required proof of purchase and other documentation.
2) Estimated Water Savings Equipment Rebate
This rebate does not require equipment to be metered and provides a lower maximum rebate amount for the equipment below. The maximum rebate amount is set per equipment type and up to 50 percent of the purchase cost, not to exceed $750,000. The SFPUC will consider rebates for Other Equipment not listed if the applicant provides sufficient evidence the equipment will save 74,800 gallons or more a year. Supporting evidence for Other Equipment may include manufacturer-published water savings information in combination with results of qualified audits, engineering designs or reports, historic water use with existing equipment, and other project-specific information. The SFPUC will determine if supporting information is sufficient. Rebate amounts for Other Equipment will be calculated at a rate of $1 per 748 gallons of water savings over an estimated 10-year project life span. This rebate requires an onsite inspection by the SFPUC before and after the equipment is installed. The Estimated Water Savings rebate will be calculated and issued upon successful completion of a post inspection, and confirmation that of proof of purchase and other required documentation has been received. Any equipment below that can be metered to verify water savings may qualify for the higher Metered Water Savings rebate.
Equipment Type | Rebate Amount |
Cooling Tower pH Controllers | Up to $8,000 |
Medical Equipment Steam Sterilizers | Up to $2,500 |
Air-cooled Ice Machines | Up to $1,800 |
Commercial Laundry Retrofits | Up to $1,700 |
Dry Vacuum Pumps | Up to $1,000 |
Connectionless Food Steamers | Up to $545 per compartment |
Other Equipment | To be determined based on $1 per 748 gallons of water saved over 10 years, not to exceed 50% purchase cost |
Eligibility Requirements:
Projects must meet the following requirements to qualify for a potential rebate: rebate:
- Reduce indoor water use by a minimum of 74,800 gallons annually at a property served by an active SFPUC commercial retail water service account.
- Be permanent and be operated for a minimum of 10 years. If retrofitted equipment is not operated for a minimum of 10 years, the Participant may be required to reimburse the SFPUC the entire Rebate amount received.
- Meet all applicable local, state, and federal laws, regulations, and ordinances.
- Be completed within six months of the application submission date. An Applicant may request an extension of up to an additional six months before the conclusion of the initial Rebate Reservation.
- The following projects are not eligible projects: Replacement of toilets, urinals, clothes washer, showerheads or faucet aerators, which are subject to the San Francisco Commercial Water Conservation Ordinance (Board of Supervisor File Number 090226, Enactment Number 0077-09, which amended Chapter 13 A of the San Francisco Building Code); projects eligible for another SFPUC rebate program, such as outdoor irrigation or landscaping equipment; or projects using recycled water.
Click here to review the Commercial Equipment Rules and Regulations.
To Apply:
- Determine if your project meets the requirements for a Metered Water Savings Rebate or an Estimated Water Savings Rebate.
- Review the Commercial Equipment Rules and Regulations.
- Register the water account with our online Water Conservation Application System.
- Apply for the Commercial Equipment Retrofit Rebate Program online.
- Applicants are required to submit a completed W-9 form to the City Controller's Office.
The deadline for the current fiscal year 2024-2025 applications is May 1, 2025. Applications for fiscal year 2025-2026 will be accepted after May 1, 2025. For questions about the Commercial Equipment Rebate Program or assistance in completing your application, please contact our rebate team at waterconservation@sfwater.org or call the Water Conservation Section at (415) 551-4730.
The SFPUC may, in its sole discretion and authority, reject an Applicant’s application to the Program if it does not meet all eligibility requirements or include all required documentation.
The SFPUC may, in its sole discretion and authority and without notice, terminate or alter the Commercial Equipment Rebate Program at any time.
Funding is limited and Rebates are available on a first come, first served basis until funds run out or the Program terminates.
The SFPUC makes no representation or guarantees that participation in the Program will result in lower water bills.
SFPUC shall bear no responsibility or liability for the cost, expense, operation, maintenance, or repair of a Participant’s Qualifying Equipment Project. SFPUC shall likewise bear no responsibility or liability for delay in accepting an Application, rejection of an Application, or termination of the Program.
Qualifying projects may also be eligible for an energy rebate through the Food Service Technology Center.
Completed Project Examples
Following are examples of some of the many non-residential projects that received assistance through our rebate program. See the completed project list.
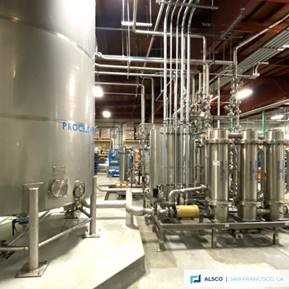
American Linen & Supply Company Commercial Laundry Efficiency Project – 1575 Indiana Street (Metered Project)
The American Linen & Supply Company (referred to as ALSCO) worked with the SFPUC to increase the water efficiency of their commercial washing machine water use. ALSCO contracted with Norchem Corporation (www.norchemcorp.com) to install an ultrapure wastewater treatment and recycling system. The Norchem system is a fully automated, modular, chemical free, patented metal oxide filtration system that is engineered specifically for wastewater treatment and energy recovery, which results in reduced water and wastewater costs. Norchem’ s membrane design maximizes flow rates at the same time reducing oil emulsions from fouling or plugging the membrane channels and treats 100% of the wastewater prior to being discharged to sewer. The system is estimated to save over 35 million gallons over the next 10 years. The project’s hardware cost was approximately $1,200,000 and ALSCO received a SFPUC commercial equipment rebate of $48,905 based on the projected water savings.
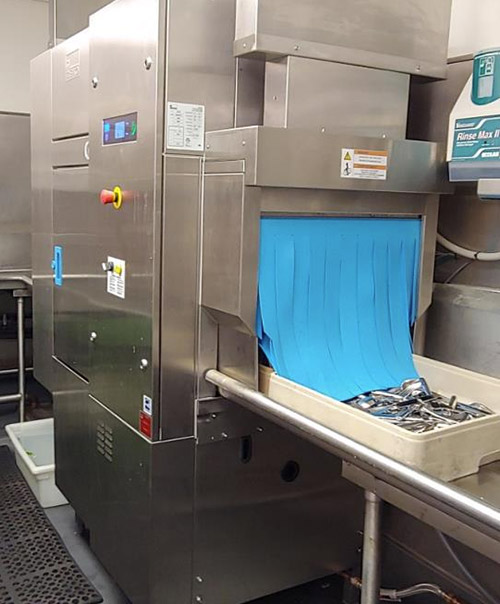
Hotel Nikko San Francisco Dish Machine Replacement Project - 222 Mason Street (Metered Project)
The Hotel Nikko San Francisco worked with the SFPUC to increase the water efficiency of their dish washing machines. Due to the high-water consumption of the old equipment, all four were replaced with new dish machines able to wash ware in over 1,300 racks per day with an annual projected water savings of 184,937 gallons per year. Some additional machine upgrades included reductions in detergent and water consumption, energy use, and final rinse of the new machines activating only when are is in the rinse zone. The new dish machines are estimated to provide over 1,849,000 gallons in water savings over a ten-year project life span. The project's hardware cost was $96,300 and Hotel Nikko SF received a SFPUC commercial equipment rebate of $2,742 based on the projected water savings.
UCSF Bulk Steam Sterilizer Replacement Project, Helen Diller Building, Mission Bay Campus - 1450 3rd Street (Metered Project)
The SFPUC partnered with UCSF to increase the water efficiency of two bulk steam sterilizers. Both sterilizers broke down regularly and were using about 12 million gallons per year. The new sterilizers are connected to the campus chilled water system to temper steam condensate. The condensate from the sterilizer flows to a return system, eliminating the tempering consumption, and returning heat energy to the campus system. In addition, the new equipment is programmed to a sleep cycle while not in use, further reducing consumption. The new sterilizers are estimated to provide 88,000,000 gallons in water savings over a ten-year project life span. The total hardware cost was $984,000, and SFPUC issued UCSF a $117,804 commercial equipment rebate.
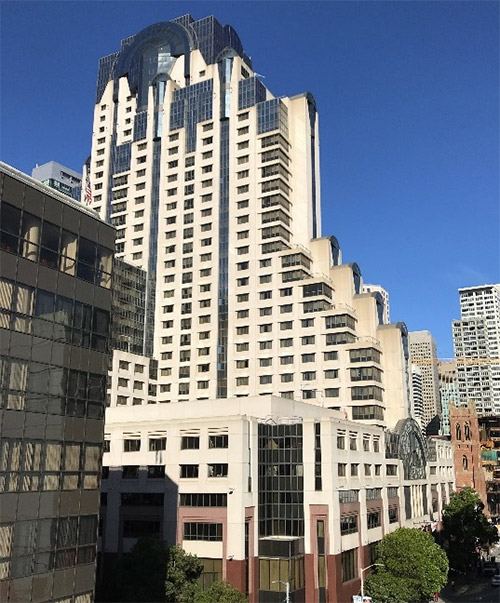
Marriot Marquis Hotel Dish Machine Project - 780 Mission Street (Metered Project)
Marriot Marquis Hotel increased the water efficiency of its associate cafeteria dish washing machine by replacing the old one with a new water efficient version, a Hobart Model CLPS66E. Based on the estimated project life span of 10 years, the lifetime water savings in combination with the total project hardware cost were used to calculate the rebate amount. The project resulted in 262,000 gallons per year and received a $3,510 commercial equipment rebate from the SFPUC.
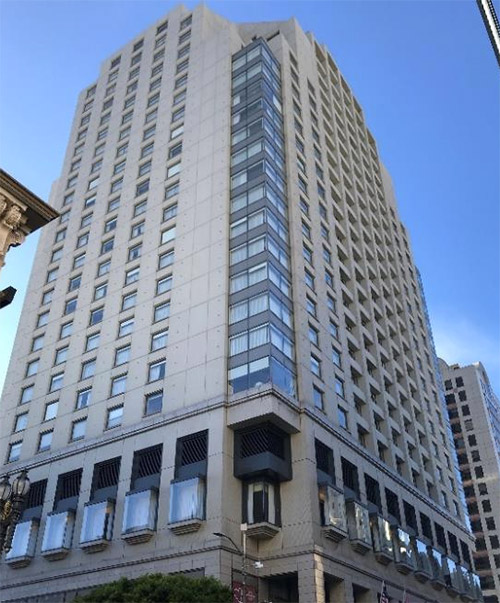
Hotel Nikko San Francisco Water Cooled Ice Machine Replacement Project - 222 Mason Street (Estimated Project)
The Hotel Nikko increased the water efficiency of its ice-making operations by replacing 19 inefficient water-cooled ice machines with air-cooled machines. Once through water-cooled ice machines use cold water to cool the condenser and then the water is dumped down the drain, resulting in significant water waste. Water consumption of once-through water cooled ice machines is 8 times greater than air-cooled machines and water savings is estimated at 129 gallons per machine per day for each air-cooled model replaced (an 89% reduction of condenser cooling water use) or 895,000 gallons per year collectively. Based on project cost and water savings, the hotel is slated to receive a SFPUC commercial equipment rebate of $32,400.
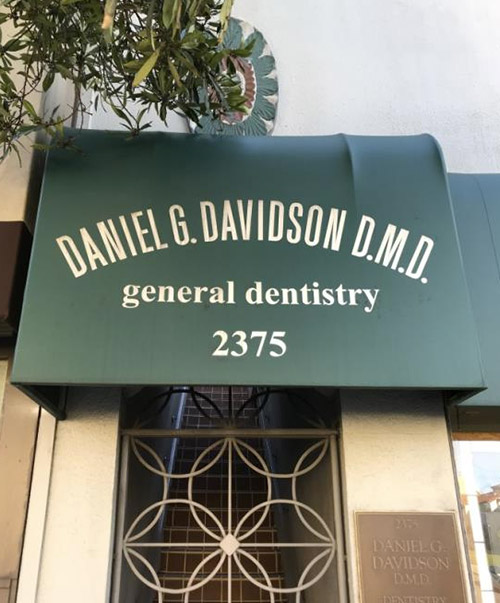
Davidson Dental Dry Vacuum Project - 2375 Ocean Avenue (Estimated Project)
Dr. Daniel Davidson found that the vacuum pump supplying suction to his dental office was performing poorly, resulting in problems with the vacuum lines and impacts to daily operations. Davidson Dental worked with Yaeger Dental Supply to specify a new dry vacuum pump that would use no water and reduce water demand by 120,000 gallons per year. The TSV-5 Dry Dental Vacuum by Toppen Solutions, LLC was installed to replace the old, inefficient liquid ring vacuum. The SFPUC provided a $1,000 rebate.
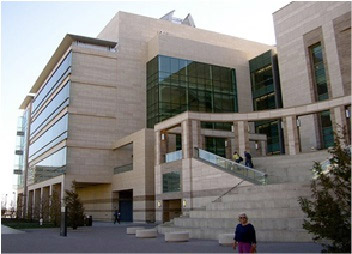
UCSF Sterilizer Replacement Project, Genentech Hall, Mission Bay Campus - 600 16th Street (Metered Project)
UCSF significantly increased water efficiency of its Genentech Hall sterilizers. The project replaced seven old 120 Century sterilizers with new Gentinge 533LS-E water efficient sterilizers. The new sterilizers were purchased for a hardware cost of $326,000 with additional installation costs of $349,000 for a total project cost of $675,000. Pre and post water metering shows an average water savings of 18,000 gallons per day or 6,489,000 gallons per year. Based on the estimated 10 year project life water savings of 64,388,000 gallons and the project's hardware cost, the SFPUC issued UCSF a $86,080 commercial equipment rebate.
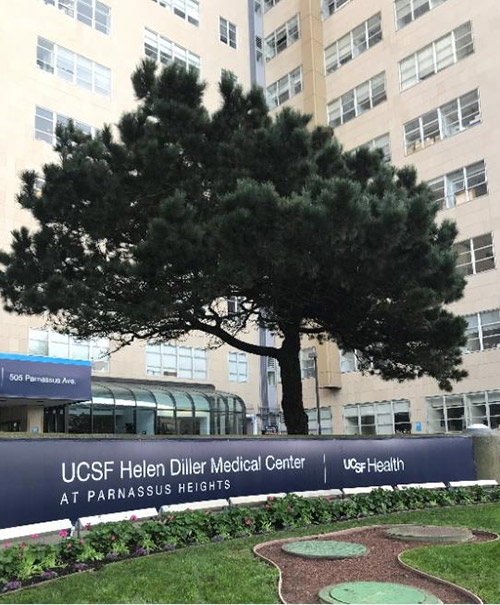
UCSF Sterilizer Replacement Project, Hooper Lab, Parnassus Campus - 505 Parnassus Avenue (Metered Project)
UCSF increased the water efficiency of the Parnassus Campus Hooper Lab's equipment sterilization process. The project replaced an old sterilizer used to clean laboratory glassware with a new water efficient sterilizer. The UCSF Parnassus Campus Hooper Lab was equipped with a new Gentinge Model 533LS-E Sterilizer. Based on the estimated 10 year project life water savings of 5,387,400 gallons and the project's hardware cost of $37,415, the SFPUC issued UCSF a commercial equipment rebate of $7,202.
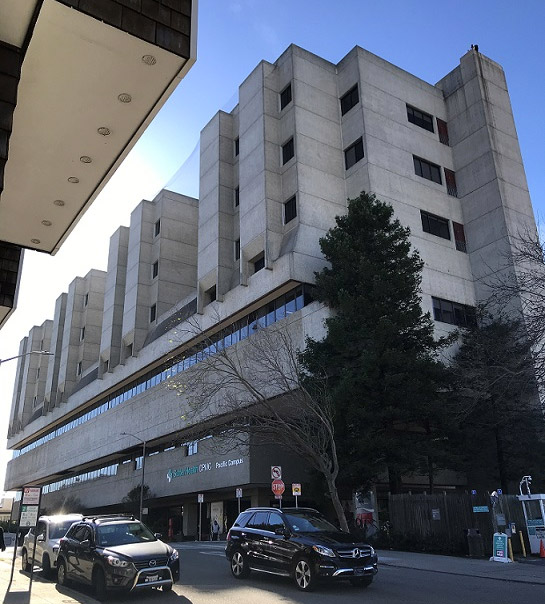
Sutter Health Refrigeration Efficiency Project - 2333 Buchanan Street (Metered Project)
Sutter Health's California Campus converted four compressor-maintained walk-in coolers and freezers that store perishable goods. The original inefficient cooling approach caused water to flow through the condenser section of each unit and then to the drain. The completed project converted the once-through cooling design to a closed loop cooling design. The water-cooled condensers at each unit were connected to the chilled water central plant condenser water loop supply and return lines located directly outside the door to the room where they are located. A small electric circulation pump was installed to supply roughly 2 gallons per minute required by each condenser. Isolation valves were installed for condenser servicing and balancing valves were installed to insure proper flow at each condenser. With a total project cost of $108,000 and an annual water savings of 4.35 million gallons, the SFPUC provided a $17,407 commercial equipment rebate.